Automotive 3D Printing Market Expected To Achieve USD 15.8 Bn In Revenues By 2032, Driven By 22.4% CAGR
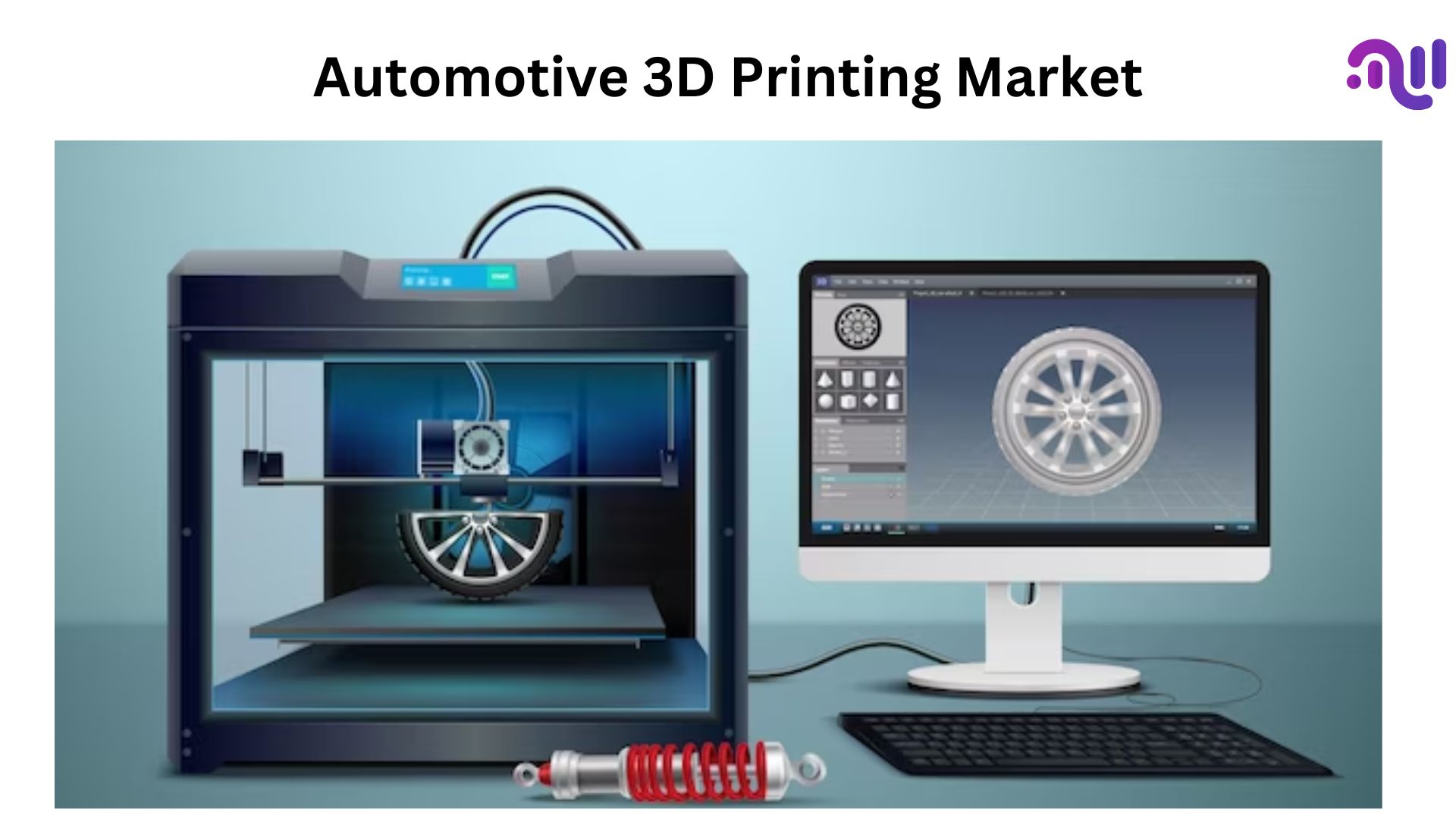
Page Contents
Market Overview
Published Via 11Press : The Automotive Technology Market has undergone impressive advancements over time, and one technology that has proven especially noteworthy is 3D printing. The automotive 3D printing market refers to using additive manufacturing techniques for producing parts, components, and prototypes in cars.
The Automotive 3D Printing Market Size Was To Reach USD 2.2 Billion In 2022 And is Projected To Reach a Revised Size Of USD 15.8 Billion By 2032, Growing At A CAGR of 22.4%
3D printing (also referred to as additive manufacturing) involves creating three-dimensional objects by layering material in an additive fashion. This technology offers several benefits for automotive industries including design flexibility, cost reductions, faster production cycles, and the creation of complex geometries.
The automotive 3D printing market has experienced extraordinary expansion for various reasons. Automakers use 3D printing technology to optimize component designs, which ultimately results in lighter and more energy-efficient parts resulting in reduced emissions and enhanced fuel economy. This contributes significantly to overall market expansion.
Download Your Guide: Explore the Rapid Growth Potential of the Automotive 3D Printing Market – Get Our PDF Sample Report@ – https://market.us/report/automotive-3d-printing-market/request-sample/
Key Takeaways
- Advancements in Technology: 3D printing technology has advanced exponentially over recent years, enabling more efficient and cost-effective production of automotive parts. It allows complex designs to be created without resorting to conventional manufacturing processes – something traditional manufacturing techniques simply cannot match up against.
- Customization and Personalization: 3D printing provides automotive companies with the ability to tailor vehicles and parts according to individual customer preferences, leading to higher customer satisfaction ratings as well as greater market competitiveness.
- Supply Chain Optimization: 3D printing has the power to revolutionize automotive supply chains by cutting inventory costs and lead times significantly. Instead of having to depend on an intricate network of suppliers for parts production, manufacturers can produce parts on-demand without incurring storage or transportation fees.
- 3D Printing's Lightweighting and Material Efficiency Advantages: 3D printing allows the creation of lightweight components without compromising strength or performance, which in turn improves fuel economy while simultaneously decreasing emissions for vehicles that are more eco-friendly. In addition, material utilization optimization using this process reduces waste while improving sustainability.
- Rapid Prototyping and Iteration: 3D printing allows manufacturers to perform rapid prototyping and iteration on automotive designs, providing manufacturers with quick production cycles to test prototypes that allow for easier identification of flaws or improvements and accelerate product development cycles as well as cut time-to-market timelines.
Automotive 3D Printing Statistics
- The Automotive 3D Printing Market is projected to reach USD 15.80 Billion by 2032.
- This growth represents a remarkable 22.40% Compound Annual Growth Rate (CAGR) from 2023 to 2032.
- In 2022, the market was valued at USD 2.2 Billion.
- 3D printing is a cutting-edge technique for manufacturing automotive parts.
- It involves using specialized printers to create three-dimensional objects using materials like metals, plastics, and composites.
- Key drivers for market growth include the demand for lighter vehicles, reduced production costs, and quicker development cycles.
- Original Equipment Manufacturers (OEMs) are increasingly adopting 3D printing to streamline production.
- Investment in research and development for 3D printing in manufacturing is a significant trend.
- Improved materials and processes have expanded the possibilities of 3D printing.
- Challenges include price fluctuations in engine oil and increased competition.
- Untapped markets offer growth opportunities for the automotive 3D printing industry.
- Recent trends include using 3D printing for prototyping and sustainable manufacturing.
- The prototype and tooling segment is the most profitable in the market.
- Production application is expected to grow significantly.
- Fused Deposition Modeling (FDM) is the largest segment in terms of revenue share.
- Selective Laser Sintering (SLS) is the fastest-growing technology.
- Plastic materials dominate the market due to their cost-effectiveness.
- Metal 3D printing is also experiencing rapid growth.
- Internal Combustion Engine (ICE) vehicles have a higher market share than electric vehicles.
- Electric vehicle demand is growing, particularly for specialized parts.
- Hardware offerings are the most lucrative segment in the market.
- Software offerings are expected to grow at a fast pace.
- Exterior components dominate the component segment.
- Interior components are the fastest-growing segment.
- North America holds the largest market share at 38.9%.
- Asia Pacific is the fastest-growing region, with a CAGR of 21.8%.
- Key players include 3D Systems Corporation, Autodesk Inc., and Stratasys Ltd.
- ExOne’s parent company, Desktop Metal, secured a US$9 Million order.
- ALM and 3D Systems partnered to offer DuraForm PAx material.
- Stratasys Ltd. completed a merger with Ultimaker.
Facts About Automotive 3D Printing
The automotive 3D printing market has seen significant advancements and growth in recent years, with a wide range of applications from prototyping and tooling to the manufacturing of complex components. Here are some key facts and figures that highlight the current state and potential of 3D printing in the automotive sector:
- North America has been the largest region for automotive 3D printing in 2022 and is expected to continue leading in innovation and adoption of this technology.
- Key technologies in the automotive 3D printing market include Stereolithography (SLA), Selective Laser Sintering (SLS), Electron Beam Melting (EBM), Fused Deposition Modeling (FDM), and Laminated Object Manufacturing (LOM), among others.
- FDM is particularly noted for its versatility in creating prototypes, concept model parts, and finished products.
- Materials used in automotive 3D printing span metals, plastics, composites, and resins, with polymers being the most commonly utilized material due to their strength and flexibility. However, there is a growing use of metals for parts requiring high pressure and temperature endurance.
- Some of the most exciting 3D printed cars and supercars include the EDAG Light Cocoon, Nanyang Venture 8, Local Motors Strati, Polymaker LSEV, and PUV ORNL 3D Printed Car, each showcasing different aspects of how 3D printing technology can revolutionize automotive design and manufacturing.
Drivers
- Design Flexibility: 3D printing affords designers an unprecedented degree of creative freedom and design versatility that traditional manufacturing cannot match. 3D printers allow the creation of complex geometries which lead to improved performance, lightweight, and optimization in parts – as well as customizable innovations favored by automobile companies where customization and innovation play such an essential part of success.
- Cost Efficiency: 3D printing can offer significant cost-cutting opportunities in automotive manufacturing processes. By eliminating expensive tooling and molds required in traditional production methods – especially those intended for low volume or prototyping production runs – 3D printing makes parts production on-demand possible, decreasing inventory costs while simultaneously decreasing wasteful storage fees.
- Supply Chain Optimization: 3D printing in the automotive industry can significantly streamline and optimize its supply chains and lead times, eliminating complex global chains for parts sourcing while using local production to decrease inventory levels, and transportation costs, and increase the overall efficiency of its supply chains.
- Accelerated Time-to-Market: 3D printing offers rapid prototyping and iteration for automotive designs, helping manufacturers shorten the product development cycle and get new vehicles onto the road more quickly for sale. Quicker prototype turnaround times as well as design changes on demand give automotive firms an advantage that could give them an accelerated time-to-market.
Opportunities
- Mass Production: While 3D printing has traditionally been utilized for prototyping and low-volume production, there is now an emerging opportunity in automotive mass production using this revolutionary technology. Thanks to faster print speeds and larger build volumes, 3D printing becomes ever more applicable as an industrial production strategy, potentially offering significant cost savings, greater efficiencies, and faster production cycles than alternative manufacturing techniques.
- Tool and Jig Manufacturing: 3D printing can be utilized as an efficient means for producing custom tooling and jigs used during automotive production processes. By 3D printing these tools, manufacturers can reduce lead times, enhance accuracy, and decrease costs compared to traditional tooling methods – providing greater production flexibility and efficiency on the floor.
- On-Demand Spare Parts: The automotive industry faces many difficulties when it comes to providing spare parts for older or discontinued vehicle models, making 3D printing an invaluable solution in producing spares when they are needed. 3D printing makes production faster while eliminating storage fees and shortening lead times – increasing customer satisfaction, cutting manufacturing costs, and prolonging the lifespan of vehicles all at the same time!
- Electric Vehicle (EV) Components: With the increasing adoption of EVs comes an immense opportunity for 3D printing to meet their specific manufacturing requirements. 3D printing can produce lightweight complex geometries for battery housings, motor parts, and other EV components – leading to improved performance, greater energy efficiency, and decreased weight which all are key factors in today's EV market.
Challenges
- Cost: Initial costs associated with 3D printing equipment, materials, and software can be substantial for industrial-grade printers. Furthermore, 3D printing materials like polymers or metal powders tend to cost more than traditional manufacturing materials and could act as a barrier to entry for smaller automotive manufacturers or restrict the widespread adoption of this technology.
- Material Limitations: While significant progress has been made in developing 3D printing materials for automotive use, traditional manufacturing still provides greater choices of material options than 3D printing materials do. Automotive components often need specific mechanical, thermal, and chemical properties that must be fulfilled; finding suitable 3D printing materials which meet those demands can be challenging; thus restricting its applicability for some components or applications of auto manufacture.
- Production Speed: While 3D printing offers many design flexibility and customization advantages, its production speeds tend to lag behind traditional manufacturing processes. Crafting complex parts layer by layer takes more time, which may impede overall efficiency for high-volume manufacturing operations. Furthermore, improving print speeds without compromising quality remains a significant challenge within automotive 3D printing markets.
- Scale and Size Limitations: When it comes to manufacturing larger automotive components like chassis or body panels with 3D printers, their size limits present unique challenges when trying to scale production up efficiently and cost-effectively. Scaling production involves many technical steps which require specialist equipment and expertise – overcoming these limitations is a continual endeavor and remaining cost-effective production remains an ongoing battleground.
Market Segmentation
Based on Application
- Prototyping & Tooling
- Research Development & Innovation
- Production
- Other Applications
Based on Technology
- Stereo Lithography
- Selective Laser Sintering
- Electronic Beam Melting
- Fused Deposition Modeling
- Laminated Object Manufacturing
- Three-Dimensional Inject Printing
- Other Technologies
Based on Materials
- Metals
- Stainless Steel
- Titanium
- Aluminium
- Metal Alloys
- Plastic
- Acrylonitrile Butadiene Styrene
- Polylactic Acid
- Nylon
- Composites and Resins
- Other Materials
Based on Vehicle Type
- ICE Vehicles
- Electric Vehicles
By Offering
- Hardware
- Software
By Component
- Interior Components
- Exterior Components
Key Players
- 3D Systems Corporation
- Autodesk Inc.
- Desktop Metal Inc.
- EOS GmbH
- General Electric Company
- Hoganas AB
- Materialise NV
- Stratasys Ltd.
- Ultimaker BV
- Voxeljet AG
- ExOne Company
- Arcam AB
- Renishaw plc.
- HP
- com
- SLM Solutions Group AG
- Farsoon Technologies
- Sinterit
- Protolabs Electronics Pvt. Ltd.
- Nexa3D
- EPlus3D Tech GmbH
- Other Key Players

The team behind market.us, marketresearch.biz, market.biz and more. Our purpose is to keep our customers ahead of the game with regard to the markets. They may fluctuate up or down, but we will help you to stay ahead of the curve in these market fluctuations. Our consistent growth and ability to deliver in-depth analyses and market insight has engaged genuine market players. They have faith in us to offer the data and information they require to make balanced and decisive marketing decisions.